The bolts in the wind power tower bear the alternating load of tension and compression, and bear the fatigue load at the same time. The traditional flange form is thick forged flange. The advantages of this flange are
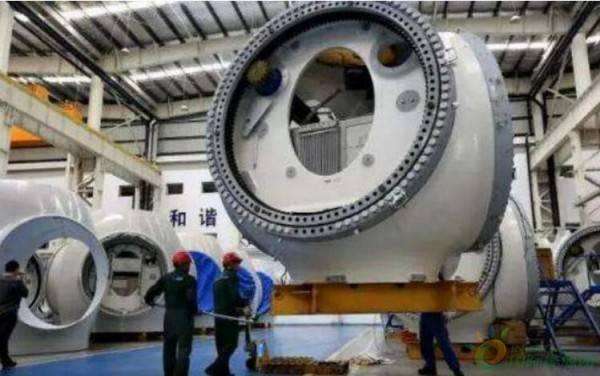
less welds, long bolts, good fatigue resistance and large flange stiffness. However, this kind of flange also has its own shortcomings: the cost is too high, the manufacturing energy consumption is large, the end face needs to be milled, the material consumption is large, and the screw hole deviation is not easy to deal with. A large number of are imported, and there are still bolt looseness problems, which need to be tested and maintained every year. Moreover, regular maintenance can not fully ensure the reliability of the connection. Repeated tightening of high-strength bolts will cause changes in the crystal structure of the thread. Due to the increase of torque coefficient, the torque specified in the specification can not reach the pre tension specified in the specification. In order to achieve pre tension, the torque is excessively increased, so that the bolt produces plastic deformation or even fracture under the action of external force. Once the bolts in key parts fail due to looseness, it may cause huge losses. The analysis shows that there are three reasons for bolt loosening:
1) Generally, Dacromet coating is used as the anti-corrosion method for bolts, but this will lead to unqualified bolt torque coefficient. Therefore, molybdenum disulfide coating is used to reduce the torque coefficient in engineering. However, doing so will halve the friction coefficient of bolt thread and reduce the self-locking ability of bolt;
2) This kind of bolt is generally constructed by torque method. Because the torque method applies pre tension to the bolt by tightening, the bolt is torsional deformed in this process, and there is torque in it. When the external torque is removed after the construction is completed, part of the torsional elastic potential energy, that is, rebound torque, will be stored in the bolt.
3) Under the action of wind load, the tension of the bolt on the leeward side decreases and the pressure on the thread surface decreases. After the friction torque to prevent the bolt from loosening is less than the rebound torque, the bolt will loosen. When the bolt becomes loose, the high-strength bolt becomes an ordinary bolt. Under the action of wind load, the fatigue stress amplitude of the bolt will be significantly increased, and the stress amplitude of the bolt will resist all external forces and bending moments.
Generally, the threaded connection has a certain self-locking property and will not loosen by itself when subjected to static load and little change in working temperature. However, under the action of impact, vibration or variable load, and when the working temperature changes greatly, the threaded connection will become loose, resulting in accidents. In order to ensure the safety and reliability of threaded connection, effective anti loosening measures must be taken for threaded connection. Common methods include eccentricity, steel sheet, lock sheet, slotting, double lamination, nylon and so on. However, these anti loosening methods are rigid anti loosening methods, which do not completely solve the essential problem of loosening. In essence, these anti loosening methods only delay the time of thread loosening, and the loosening of threaded connection is inevitable.